Title: Optimization of CDQ
Client: tkIS
Software used: Mechanical Ansys
Duration: 3 Months
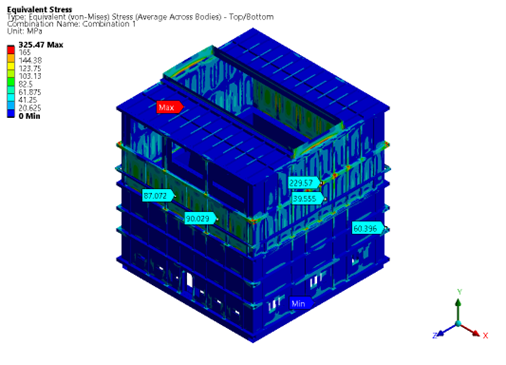
Keywords: CDQ, bunker, ASME, optimization, granular mass, coke
Quenching of coke is carried out after the cooking process. The CDQ (Coke Dry Quench) replaces the earlier wet quenching process. CDQ has gained popularity due to stricter environmental rules and water conservation being the need of the hour. The equipment of CDQ typically consists of two vertically arranged rectangular chambers or bunker. The top and bottom chambers have hopper like arrangement for the flow of coke downwards. The cooling gases pass through the coke in the bottom chamber and is carried by ducts to further process. The entire chamber assembly is mounted on a support structure. The existing structure is to be redesigned and optimized for a higher capacity of quenching. The optimization of the CDQ chambers is possible with a right combination of wall thickness and stiffener arrangement. Initially mechanical design calculations are performed based on the Rankine’s theory for pressure of granular mass on the vertical and inclined walls. The wall thickness and stiffener arrangement thus derived is the basis of optimization by FE analysis. The chambers are optimized individually and are then combined to check the effect of wind, snow and seismic loads in an integral model. The load combinations and qualification is performed as per the ASME Section VIII, Div. 2, Part 5 methodology. A 25% reduction in the weight of the chambers and an overall reduction of 12% in the weight of the equipment is achieved.
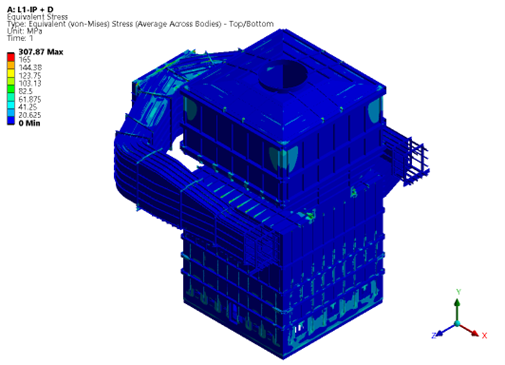
Benchmark: Application of Rankine’s theory for the pressure of the granular mass on the walls in FE analysis. Performing FE with a modular approach and integrated FE analysis for the combined effect enabled an efficient optimization process.
Recent Projects