Title: Elbow Analysis to Simulate Proof Test
Client: SES
Software used: Ansys Mechanical
Duration: 4 Months
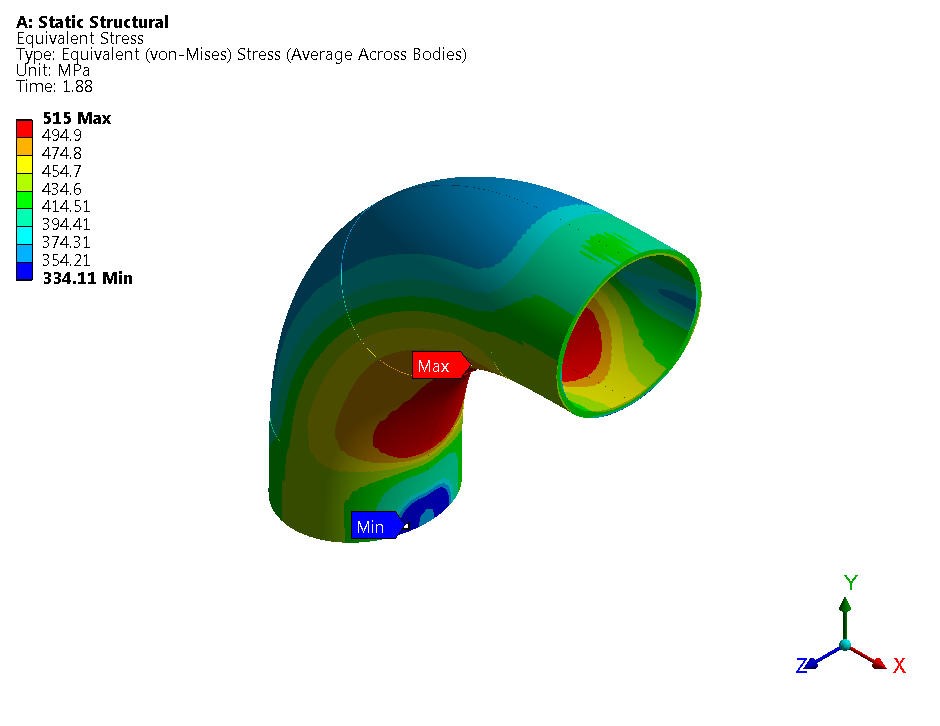
Keywords: Elbow, rupture, tensile strength, elastic-plastic analysis, ASME B16.9, convergence, true stress-strain curve.
A 24” NB elbow is manufactured from a plate by a cold-forming process in two halves. The elbow is to be checked if it can sustain the pressure applied for a proof test. The pressure for the test is derived from the actual tensile data of the material as per the guidelines of ASME B16.9. The calculated pressure is based on the actual tensile strength, the stresses induced in the elbow are higher than the yield limit of the material and may cause a rupture in some instances. Hence an elastic-plastic analysis approach is adopted for FE analysis. To perform an elastic-plastic FE analysis, the true stress-strain curve data of the material of construction is determined as per ASME Section VIII, Div. 2 Annex 3-D. The elbow is extended at both ends by pipes having a calculated pressure greater than the calculated burst pressure of the elbow. The pipes are of the same diameter and the length is equal to half the OD of the pipe. The calculated pressure is applied in gradually increasing steps. The load corresponding to the step at which, the solution is not converged is the maximum pressure sustained by the elbow before rupture. The non-convergence of solution at a step indicates structural instability. Structural instability is a result of very large deformation that occurred due to only a small increase in load. The FE analysis performed by this method enables the user to make a better decision to perform a proof test or to redesign the fitting if the results deviate from the expectations.
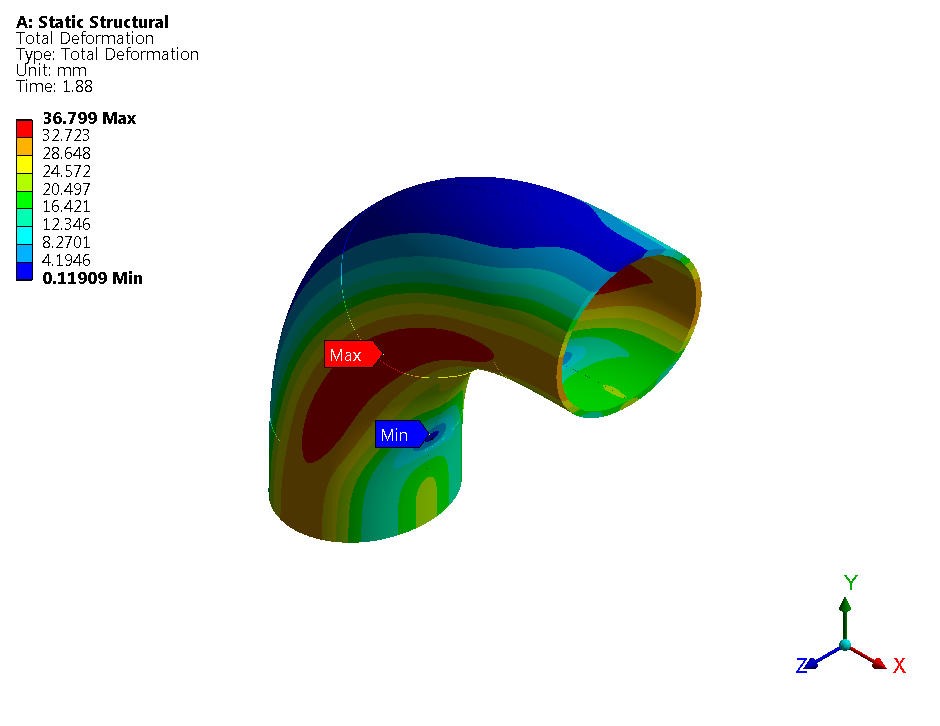
Benchmark: As the elbow was manufactured by two halves with two seams running along the elbow, it was not a standard component, and the manufacturer was required to simulate the proof test before performing the proof test. By performing elastic-plastic analysis, the maximum load before rupture was determined.
Recent Projects