Title: Root Cause analysis of flange leakage in steam recovery heat boiler
Client: SES
Software used: Ansys Mechanical
Duration: 4 Months
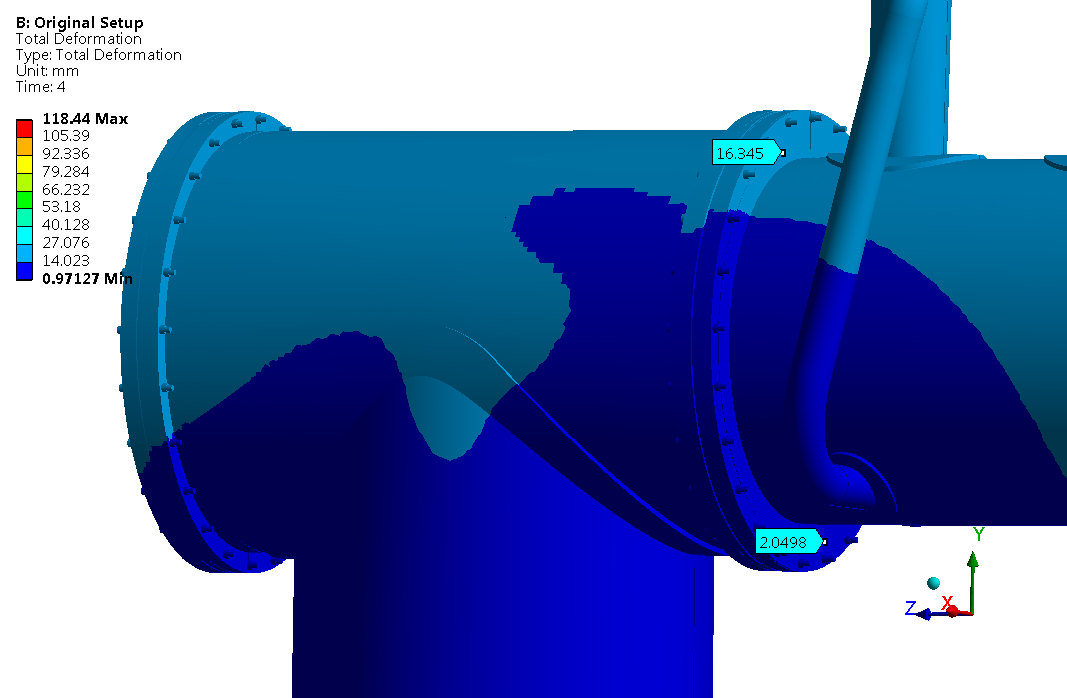
Keywords: Leakage, flange, steam recovery boiler, shell and tube heat exchanger, steam drum, spring support, downtime
A steam recovery boiler assembly consists of an incinerating boiler, shell and tube heat exchanger along with a steam drum. There are inlet and outlet ‘Tee’s’ and a number of piping connected to and from the steam drum and the boiler. Due to multi-elevation assembly and multiple piping of different sizes and temperatures connected to the boiler, the support system of the boiler is complex. The entire assembly is mounted on spring support. Though designed to accommodate the probable relative expansion, one of the flange joints was experiencing leakage. FE analysis approach is adopted to perform a root cause analysis in order to reduce the frequent maintenance of the equipment. The entire assembly is modelled as the FE domain. Initially, the FE analysis is performed simulating the present boundary conditions. Due to non-linear behaviour of spring and unsymmetrical loading, relatively high deflection is observed. Due to higher relative deflection between inlet T and heat exchanger, leakage is observed at the flange joint. Based on the deflection behaviour, FE analysis is performed with spring along with sliding support arrangement. This arrangement helped significantly to control the deflection and accommodate thermal expansion. The modifications are proposed in the support system which will reduce the maintenance of the components in the area of leakage and hence reduce the downtime of the equipment significantly.
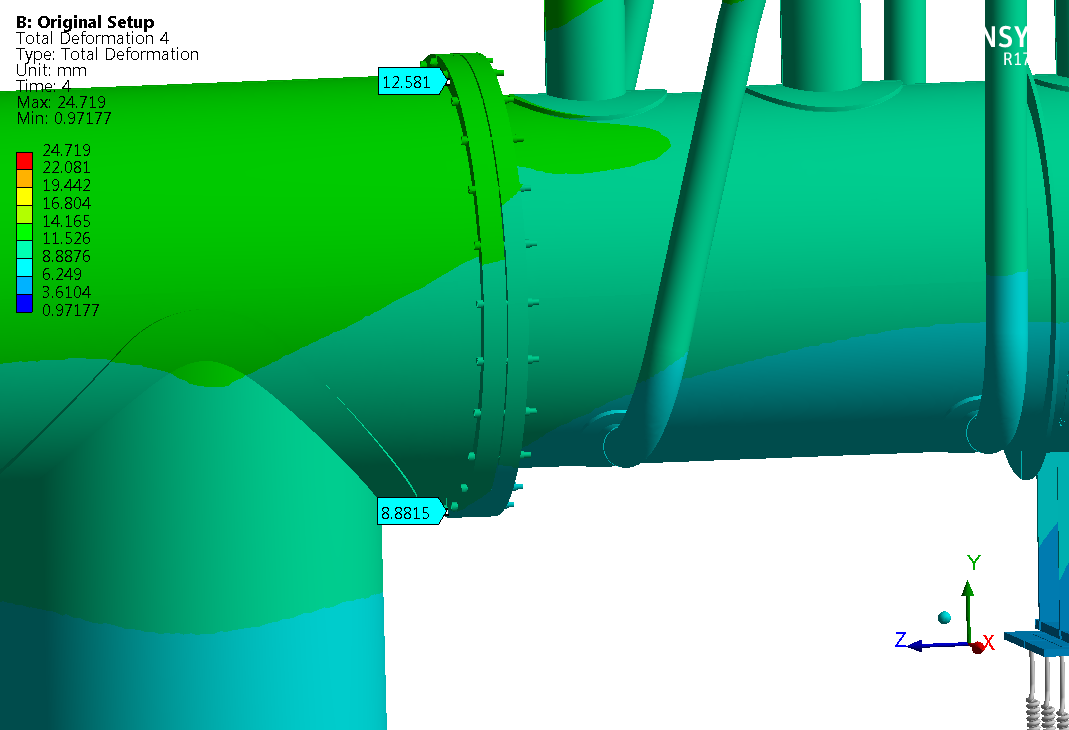
Benchmark: The cause of flange leakage in the complex equipment assembly was identified and will help the client to solve the problem of recuring replacements of the critical equipment parts.
Recent Projects