Title: Cone of Coke Drum – Fatigue Calculations
Client: IDESA
Software used: Ansys Mechanical
Duration: 4 Months
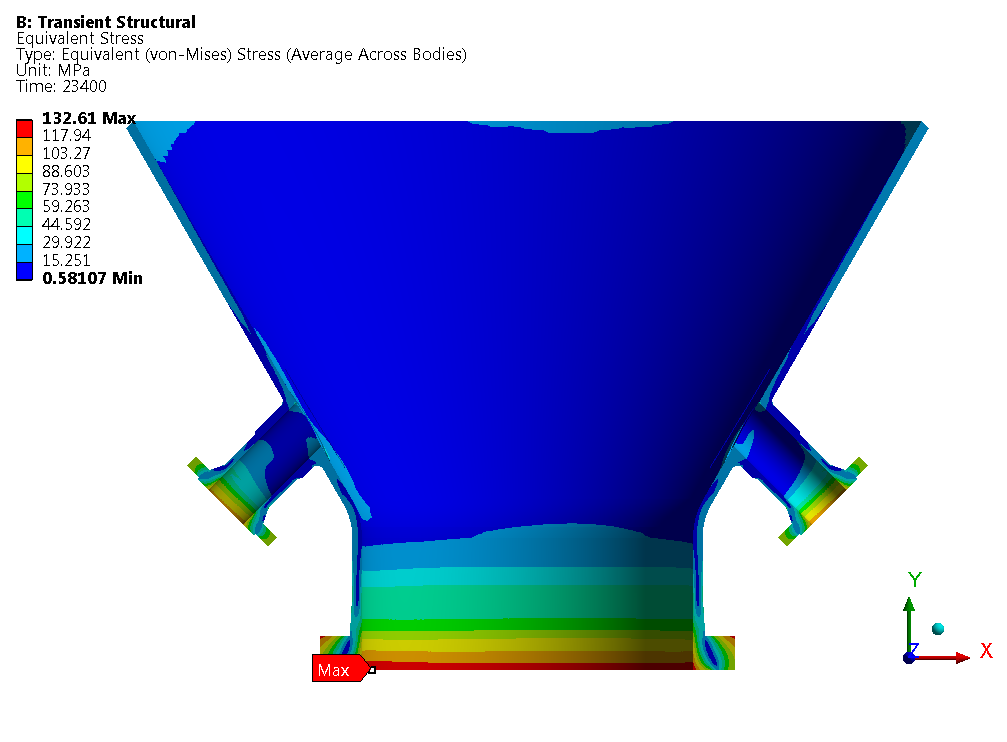
Keywords: Coke cone drum, fatigue, ASME BPVC, nozzle, fatigue penalty factor, fatigue strength reduction factor, design fatigue curve, cumulative fatigue damage.
As a part of an expansion of the oil refinery project, the bottom part of the coke drum cone is cut and replaced with the proposed design. The cone is checked with ASME BPVC Section VIII, Div. 1, while the nozzles are qualified with Div. 2 Part 5. As the components are subjected to temperature and pressure cyclic loading, cone and nozzles are critical regions prone to fatigue failure. For fatigue assessment, sequential thermal-structural analysis is performed using linear elastic material properties. Stresses at critical locations are considered for fatigue evaluation. The alternate stress is calculated from the stress range obtained from FE analysis and factors affecting the fatigue life, viz. fatigue strength reduction factor and fatigue penalty factor. The strength reduction factor compensates for any geometry feature like notch, which is not included in the FE model. The penalty factor, which imposes a penalty depending on the extent the calculated stress range exceeds the allowable equivalent stress range SPS, is also considered. The SPS is calculated based on the maximum value derived from the relation specified with allowable strength and the yield strength of the material. Once the alternating stress is calculated, the number of permissible cycles is determined from the Design Fatigue Curve given in Annex 3-F of Part 5. Comparing the design number of cycles to the number of permissible cycles, the fatigue damage is determined. The cumulative fatigue damage was found to be less than unity and hence the component safe for subjected loadings for design number of cycles.
Benchmark: Fatigue calculations are performed for critical locations as per ASME, Section VIII, Div. 2, Part 5
Recent Projects